With the booming new energy vehicle industry, environmental protection, energy saving and high efficiency have become synonymous with travel in the new era. As a firm promoter of green travel, Shenzhen Jiansiyan Technology Co., Ltd. not only leads the technological innovation of new energy electric vehicle charging piles, but also proudly owns a complete industrial chain from independent research and development, self-service production, comprehensive testing, strict aging to source sales. Among the many components, the main control board is the "brain" of the charging pile, and its importance is self-evident. Today, let us explore the unique advantages and excellent practices in this process.
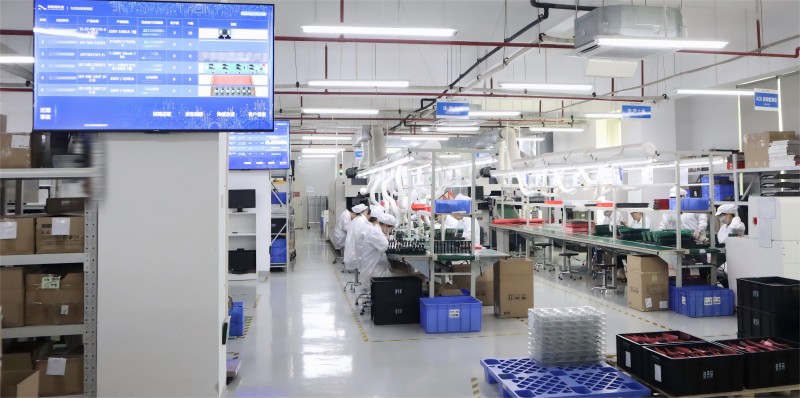
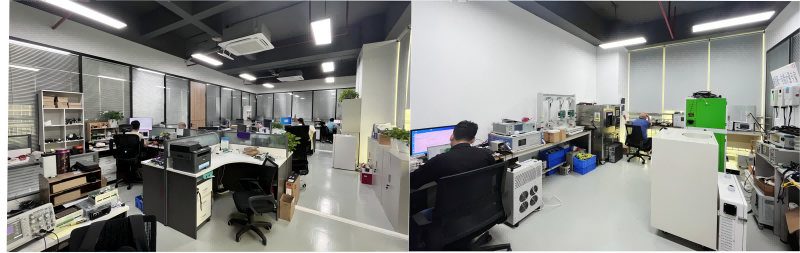
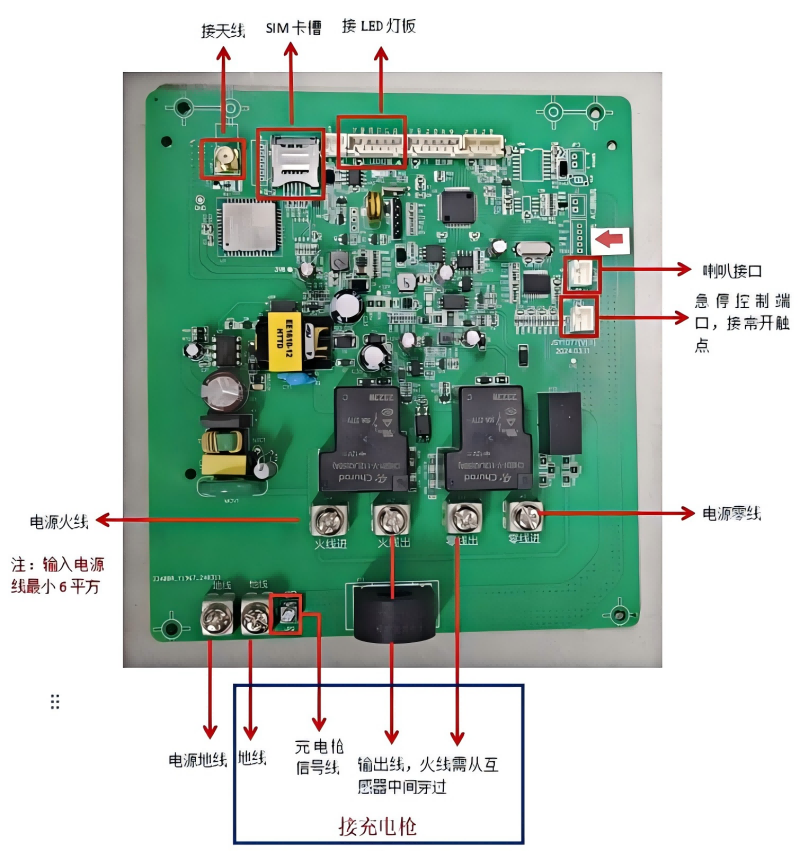
Brush solder paste
AOI Inspection
Plug-in welding
Test packaging
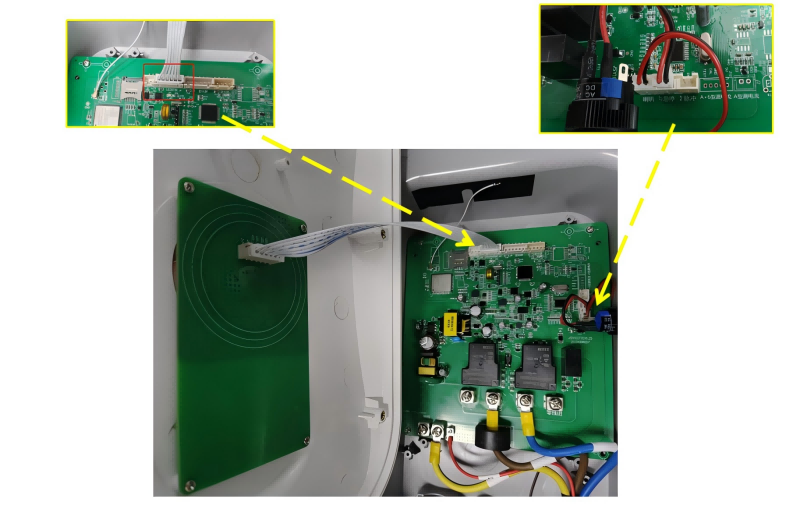
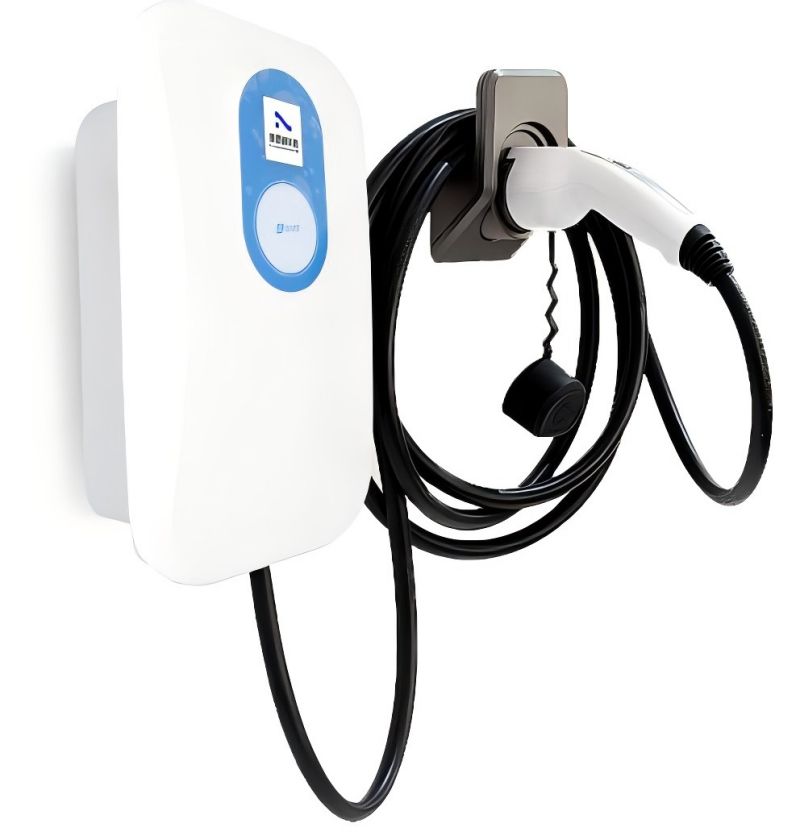
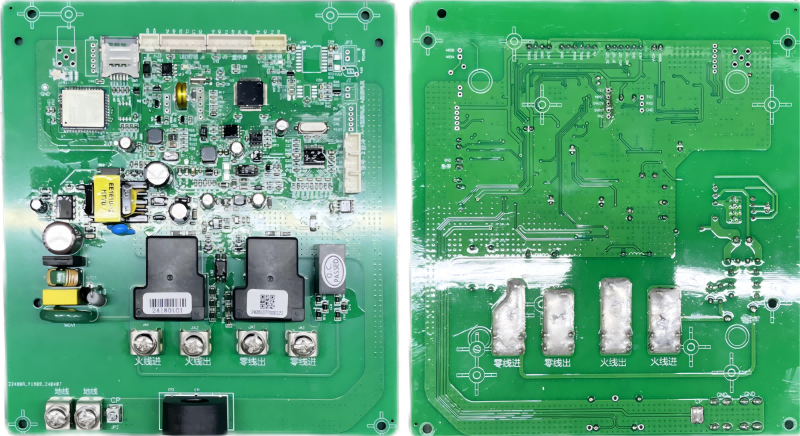
The production and installation process of the charging pile main control board is a complex system engineering that integrates precision design, fine welding, strict quality inspection, manual assembly, and comprehensive testing. Every link needs to be refined and strictly controlled to ensure the stability and reliability of the charging pile main control board during use. It is with such a high-quality "heart" that new energy vehicle charging piles can provide more convenient and efficient charging services for the majority of car owners.
Post time: Dec-28-2024